Here’s how:
Coolant, Alone, is not Enough.
We all know metal cutting produces exceptional heat that can distort and damage workpieces and tooling. Approximately 97% of the energy created by cutting, drilling, or milling metals converts to heat. That’s why metalworkers apply various coolants to reduce cutting zone temperatures. However, coolant must be used at the correct pressure and flow rate to maintain consistent temperature and lubrication, optimize tool life and allow consistently precise metal cutting.
Often, machine tools flood coolant onto the workpiece at low pressures, which can be counter-productive, as the intense heat within the cutting area causes the coolant to vaporize on contact. Flowing coolant at 1,000 PSI or greater into the machining area increases localized pressure to eliminate this problem, thus effectively reducing workpiece and cutting tool temperatures. High-pressure coolant also keeps chips at a cooler temperature so they break apart easily into smaller pieces for faster evacuation.
Therefore, correctly applying high-pressure coolant increases throughput by enabling machine tools to cut material more efficiently, reduce time spent changing tools, keep chips out of the way to prevent recutting and workpiece damage, and allow optimum spindle speeds.
Because every application has unique properties, various LNS Chipblaster high-pressure systems provide fixed and variable rate coolant delivery to match your specific requirements; fixed-rate systems are typically adequate for production using the same or similar types of material. For greater versatility in using materials and parts programming, an automatic, variable volume high-pressure coolant system allows the user to dial in the precise volume and pressure for virtually any machining application.
The LNS Chipblaster line of high-pressure systems includes:
- V-Series Variable Rate providing 40, 60, 80, or 120 Liters Per Minute at 1000 PSI
- B-Series delivers 30 Liters Per Minute at 1000 PSI
- F-Series delivers 30, 60, or 90 Liters Per Minute at 1000 PSI
- S-Series Fixed and Variable Rate with volumes of 30 and 22 Liters Per Minute at 1000 – 2000 PSI
Chip Handling is More Than Moving Metal
To some people, a chip conveyor is simply a means to move metal cuttings into a hopper. While this may be true for specific applications, in most cases, optimizing productivity requires more.
As mentioned above, adequately applied high-pressure coolant breaks up chips into smaller pieces, which makes chip removal from the cutting zone more efficient, reduces tool wear, and helps prevent workpiece damage and bottlenecks. Adding a filtering chip conveyor ensures that chips and materials of all types evacuate the cutting area flawlessly. Coolant filtration keeps fine particles from damaging sump pumps and extends coolant life.
LNS Turbo MH Series and SF Compact filtering chip conveyors use self-cleaning filtering boxes that filter coolant up to 50 microns. Turbo MF4 also filters coolant to 50 microns in a compact design that employs a unique dual conveyor system in which an upper conveyor removes heavy chunks, stringy, bushy, and large chips. A scraper-type lower conveyor removes smaller particles and deposits fines trapped by the filter drum onto an incline. All LNS filtering chip conveyors deliver virtually particle-free coolant to the machine sump.
As a result, users save money on coolant and coolant disposal fees, protect the machine sump pumping system from premature wear, and enjoy trouble-free unattended operation.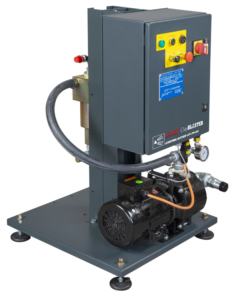
Filtering Coolant and Maintaining Coolant Tanks Should be Hassle-free
For manufacturing applications that require ultra-fine coolant filtration or when using challenging materials such as cast iron, the LNS Chipblaster CF-79 Cyclone filter has impressive filtration efficiency stats:
- Up to 100% filtering coolant to 10 microns
- Up to 95% filtering coolant to 5 microns
- Up to 50% filtering coolant to 2 microns
Moreover, Cyclonic Filtration requires no filtering media or bags that require labor-intensive maintenance. Instead, centrifugal force within the cyclone filter forces dense materials downward to the discharge port at the bottom of the filter and into the sludge tank. The Cyclone filter installs within the LNS Chipblaster high-pressure unit to save floor space, and there are no moving parts, valves, or electronics, so the system is worry-free.
The companion ST 200 sludge tank holds particulates outside the machine tool sump and is easy to clean.